Two Unique Designs to Prolong the Continuous Operation Time of Charcoal Machine
This is a subtitle for your new post
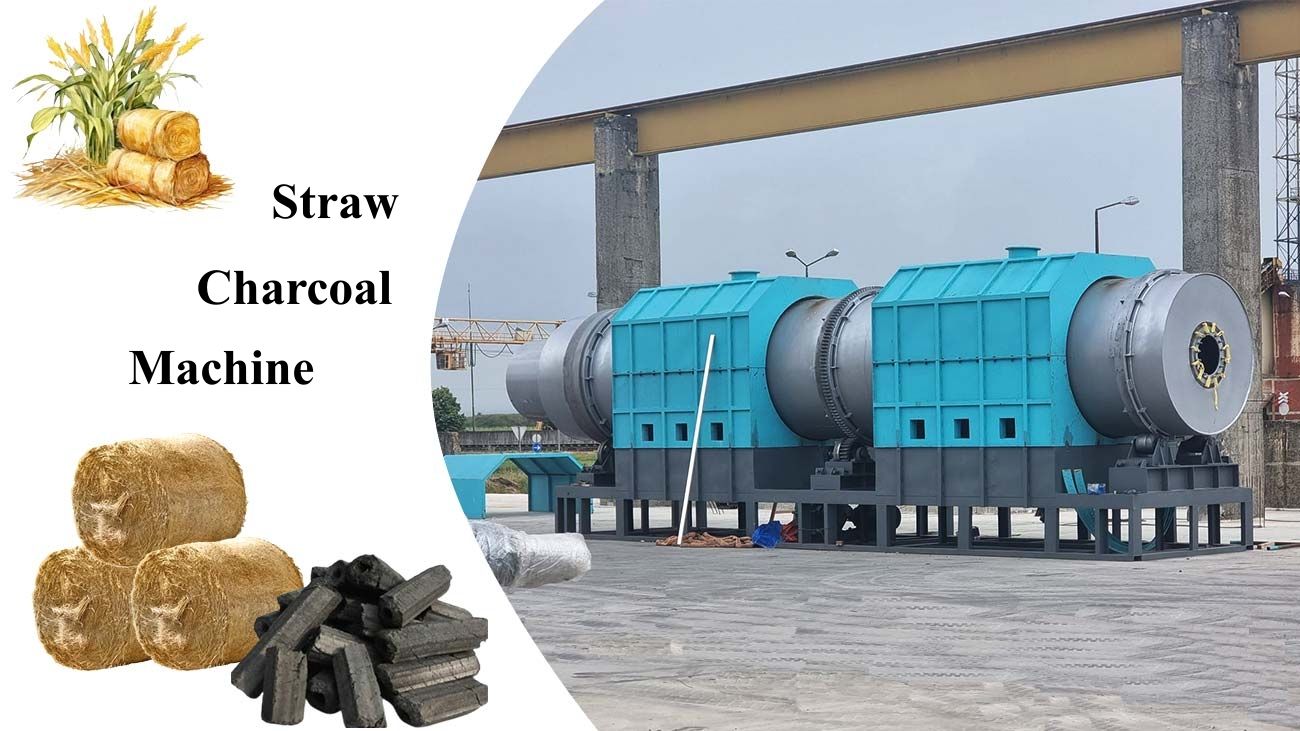
In the quest for more efficient and sustainable charcoal production, modern charcoal machines have adopted innovative designs to enhance their continuous operation time. Among these advancements, two unique features stand out: the elimination of wood vinegar and tar collection through insulation and the integration of a nitrogen purging system to prevent pipeline blockages. Let's explore these designs in detail.
1. Insulation for Eliminating Wood Vinegar and Tar Collection
One of the primary challenges in charcoal production is the collection of byproducts like wood vinegar and tar, which can disrupt the continuous operation of the charcoal machine. Traditional systems often require regular maintenance and cleaning to manage these byproducts, leading to downtime.
To address this issue, some modern charcoal machine utilize a unique insulation design. By effectively insulating the internal components, these machines maintain optimal temperatures during the carbonization process. This insulation minimizes the condensation of wood vinegar and tar within the system, allowing for their effective combustion within the machine itself. As a result, operators can experience longer run times without the need for frequent cleaning or maintenance associated with these byproducts.
2. Nitrogen Purging System for Preventing Pipeline Blockages
Another innovative design to enhance the continuous operation of charcoal machines is the incorporation of a nitrogen purging system. Pipeline blockages can occur due to the accumulation of carbonized material or condensation, which disrupts the flow of gases and reduces the efficiency of the operation.
The nitrogen purging system provides a solution by introducing nitrogen gas into the pipelines, effectively clearing any obstructions. This system operates automatically, detecting potential blockages and activating the purging process as needed. By maintaining clear pathways for gases, the nitrogen purging system ensures that the charcoal machine can operate continuously without interruptions caused by blockages. This not only enhances productivity but also contributes to the overall efficiency of the charcoal production process.
Conclusion
The advancements in charcoal machine design, particularly the elimination of wood vinegar and tar collection through insulation and the integration of a nitrogen purging system, represent significant strides toward more efficient and continuous operation. These innovations not only reduce maintenance downtime but also enhance the overall productivity of charcoal production. As the industry continues to evolve, such unique designs will play a crucial role in achieving sustainable and efficient charcoal manufacturing practices.
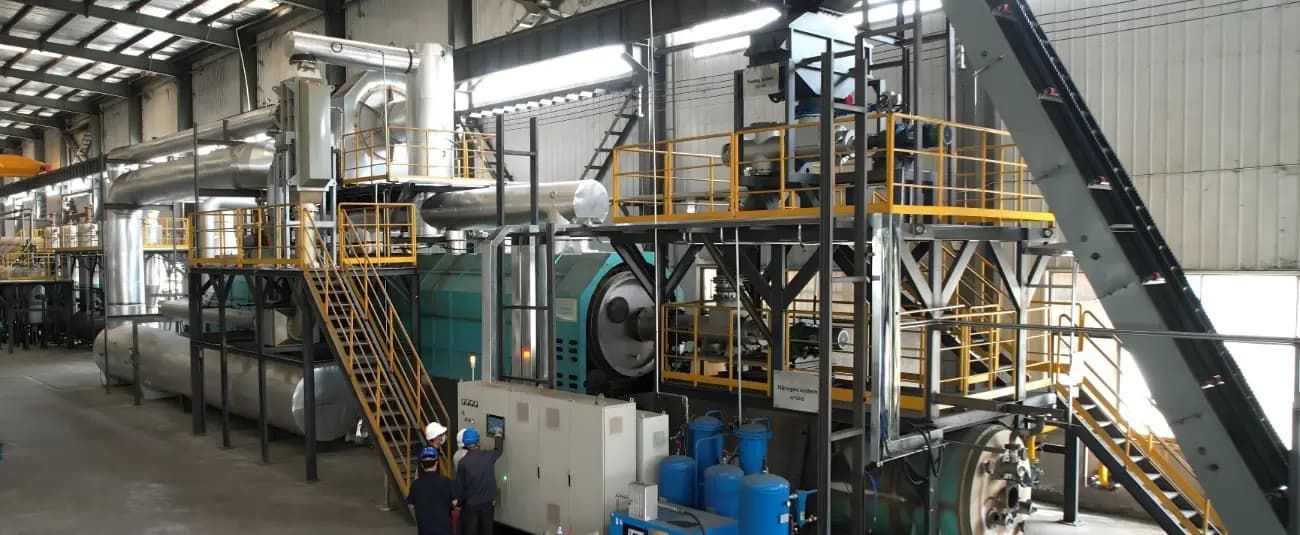
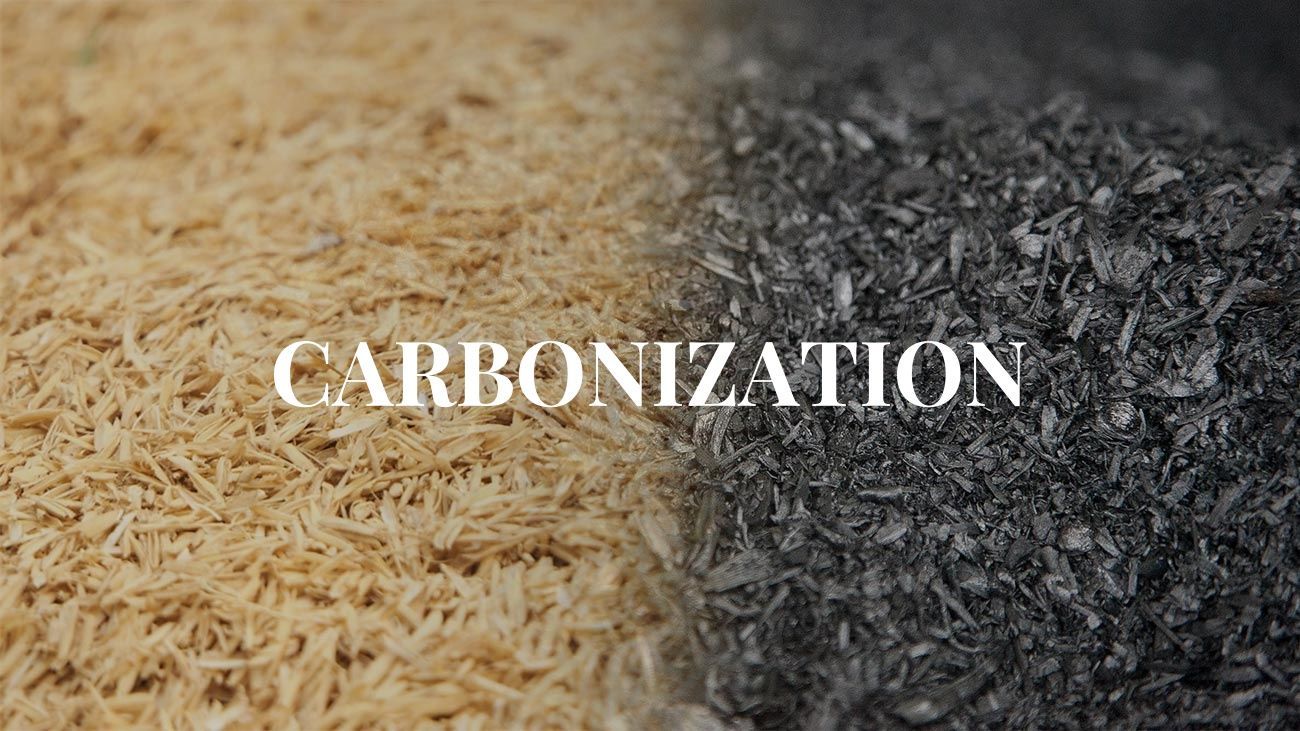
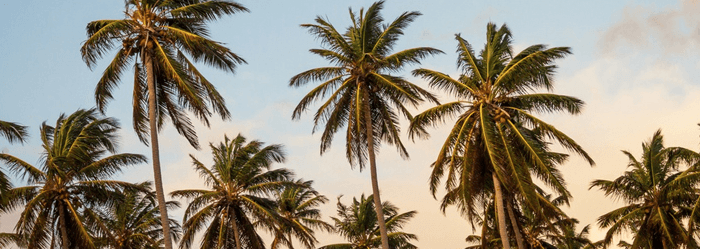