A Continuous Tyre Pyrolysis Plant Is The Simplest Way To Recycle Waste Tyres
Tyre Pyrolysis Plant
Whether you prefer it or perhaps not, in fact mankind uses a lot of items that are merely discarded once these pass their useful life. One of the greatest troubles with these discarded products is the fact that these lead to many pollution. Some of the products including plastic and tyres are incredibly harmful as harsh chemicals in these products seep into the ground water and pollute it. Waste tires can be recycled into fuel oil with waste tire recycling plant
.
Also, these are generally non-biodegradable naturally meaning that these keep lying in the landfills and do not degrade. It is estimated that the most frequent form of plastic used today takes over 1 million years to fully degrade. Because of this , that recycling of tyres and plastics has gained lots of momentum within the last decade.
Also, a number of technological breakthroughs happen to be manufactured in the recycling of waste tyres and plastic into various usable products. One of the most popular and very successful technologies on the market today for tyre recycling is called pyrolysis. Che equipment which is used just for this process is known as continuous tyre pyrolysis plant. Click here to know more: https://bestoncompany.com/
.
Tyre recycling is really a growth industry and this is the reason that there are lots of people trying to enter this business. The continuous tyre pyrolysis plant makes recycling very easy. The most significant advantages of this technology is the fact that there is absolutely no waste generated throughout the recycling process. Actually, the recycling process produces numerous valuable products including carbon black, fuel oil, hydrocarbon gases and steel wire.
Most of these goods are sought after and fetch good prices. This technology is also completely eco-friendly which means that this technique is not going to generate just about any pollution. The whole process will last for around 12 hours dependant upon the size and number of tyres. There are numerous of reputable manufacturers who build these plants with a decent price.
While it is correct that the first investment is high yet it is an extremely lucrative business. Also, it is vital that you mention here the plants made by professional manufacturers are completely safe for use and sometimes come with a safety valve together with a vacuum device in addition to other safety measures. It can do not take very long for a plant to become delivered and assembled. Get pyrolysis plant cost
here.
A lot of the professional manufacturers can deliver a whole plant in around on a monthly basis. The pyrolysis process refers back to the decomposition of organic material in the absence of oxygen. You will find three stages of the recycling process. To begin with, a feeder is used to feed the tyre pieces to the hopper. This procedure helps to ensure that there is absolutely no oxygen inside the reactor.
From the second stage, a lot of hot waste gases are generated that are passed through heat exchanger to use for even more heating the raw material. This technique runs for around 12 hours at a temperature of 300 to 400 degrees centigrade. In the last stage, the fuel oil along with other products extracted from the recycling process are pulled from the waste tyre pyrolysis plant
.
Overall, pyrolysis is actually a proven technology which is pollution free and highly affordable.
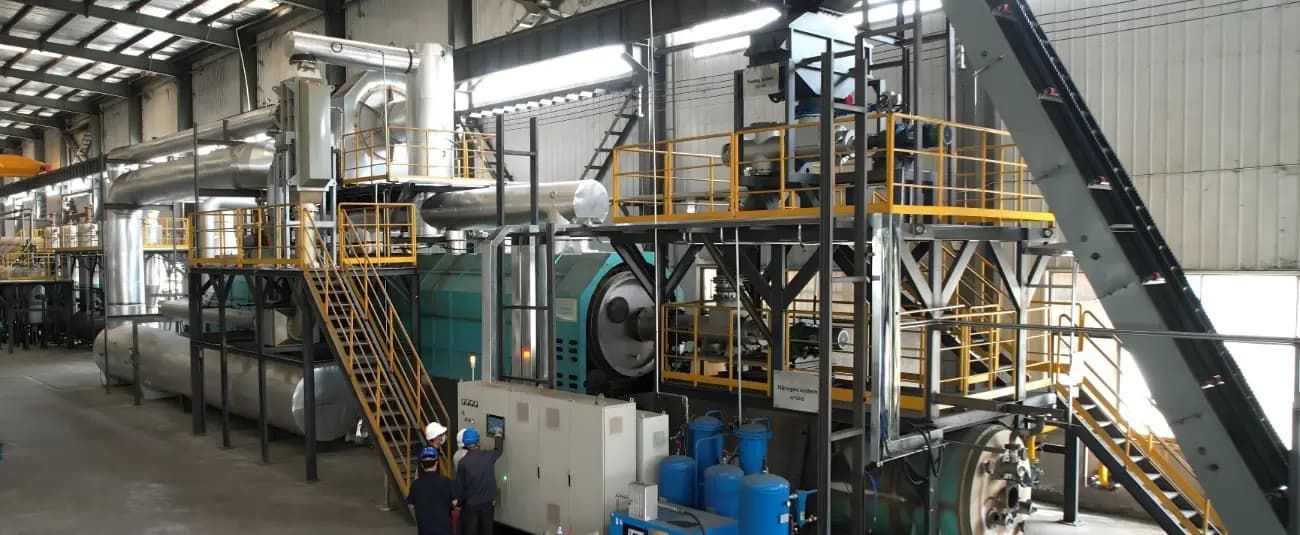
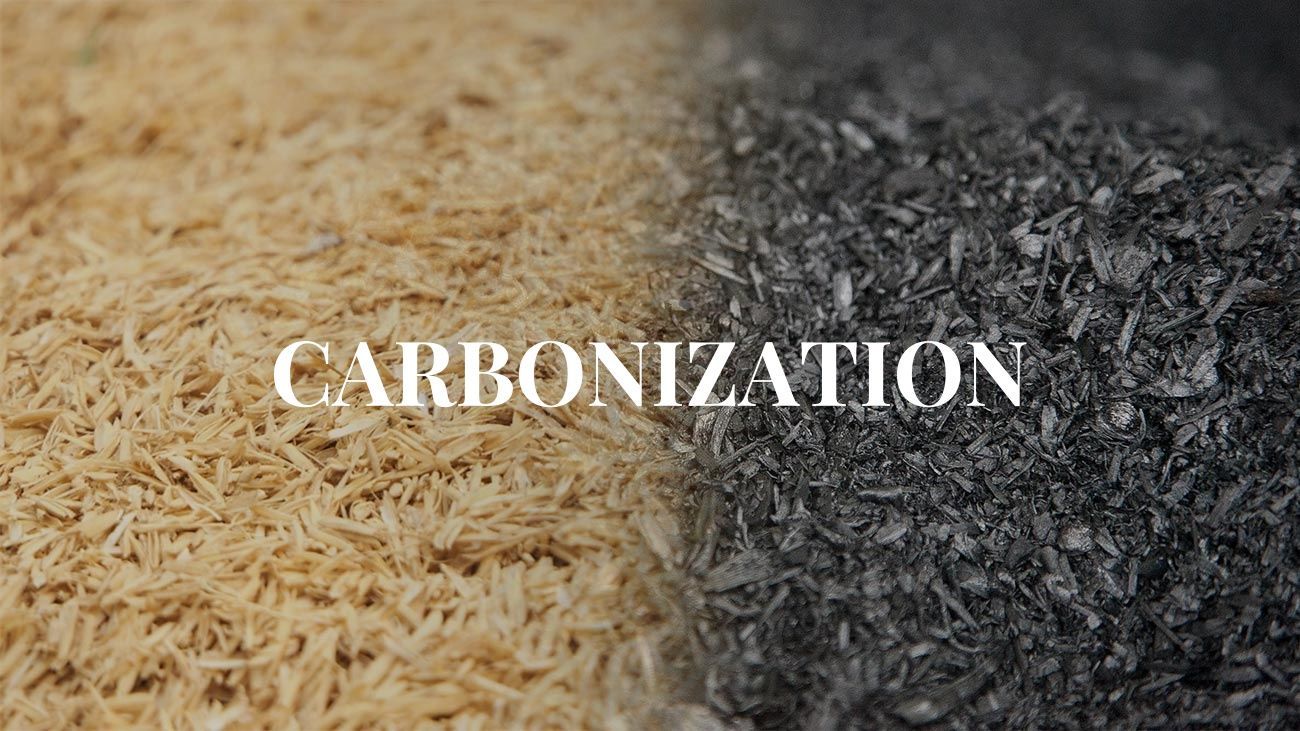
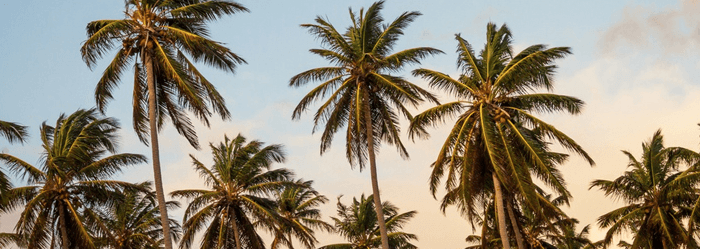