MY blog
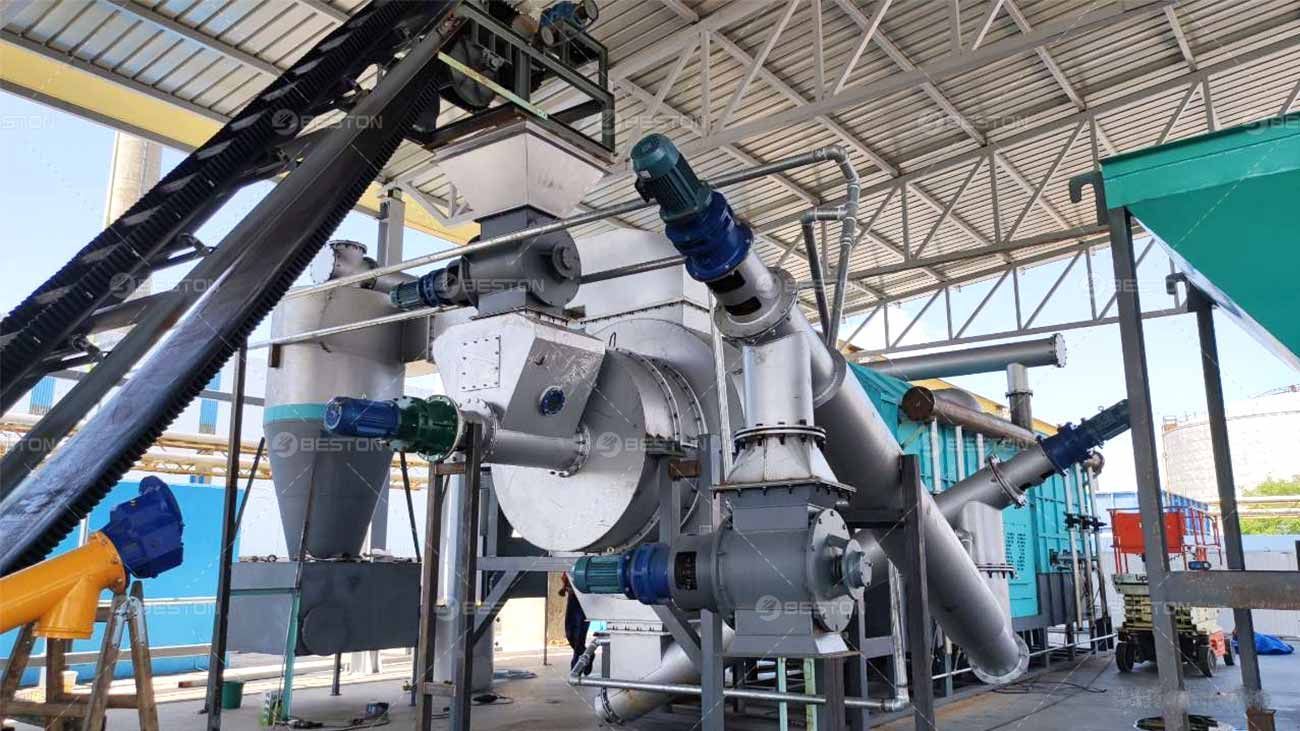
Charcoal has been a crucial energy source for centuries, traditionally made through slow-burning wood in earth-covered pits. While effective, this old-fashioned method often leads to heavy smoke emissions, low efficiency, and environmental degradation due to deforestation and air pollution. In recent years, a modern way of charcoal production has emerged, offering a cleaner, more sustainable, and efficient approach that meets both industrial demands and environmental standards.
At the heart of this modern transformation is the biomass pyrolysis technology. Unlike the traditional methods that rely on uncontrolled burning, modern charcoal production uses specialized equipment known as biomass carbonization machines. These machines operate under a condition of limited oxygen, turning organic waste such as wood chips, coconut shells, bamboo, sawdust, and even agricultural residues into high-quality charcoal through a process called pyrolysis. This process not only reduces emissions but also ensures a higher yield and consistent quality of the final product.
One of the most striking advantages of modern charcoal production machine is its eco-friendly nature. During pyrolysis, volatile substances are released in the form of combustible gas, which can be collected and reused as a heating source within the system. This closed-loop design not only saves energy but also minimizes the release of harmful gases into the atmosphere. Some advanced systems are even equipped with flue gas purification systems that filter out dust and harmful components, ensuring compliance with increasingly strict environmental regulations.
Furthermore, modern charcoal production has opened the door to the circular economy. Instead of cutting down trees, many producers now use waste biomass materials, giving a second life to what was once considered worthless. This not only reduces pressure on forests but also offers a profitable way to manage agricultural and forestry residues. For regions with abundant biomass waste, such as palm shells, rice husks, or sugarcane bagasse, charcoal production becomes an efficient method of waste-to-energy conversion.
The economic potential of this modern process is another reason it is gaining popularity worldwide. From small-scale producers to large industrial facilities, the demand for biochar is growing in various fields such as agriculture, metallurgy, water purification, and even cosmetics. The versatility and high calorific value of modern charcoal make it a desirable alternative to fossil fuels in many applications.
With the help of automation, the entire production process has become safer and more labor-efficient. Modern charcoal machines are often equipped with PLC control systems, allowing for precise temperature regulation, moisture monitoring, and production tracking. This level of control helps ensure consistent product quality and reduces operational risks.
As the world continues to seek sustainable solutions to energy and waste challenges, modern charcoal production represents a practical and forward-thinking approach. It reflects how innovation can transform traditional industries into environmentally responsible enterprises. Whether you're an investor, an environmentalist, or simply someone interested in renewable energy, the evolution of charcoal production is a compelling example of how technology can drive positive change.
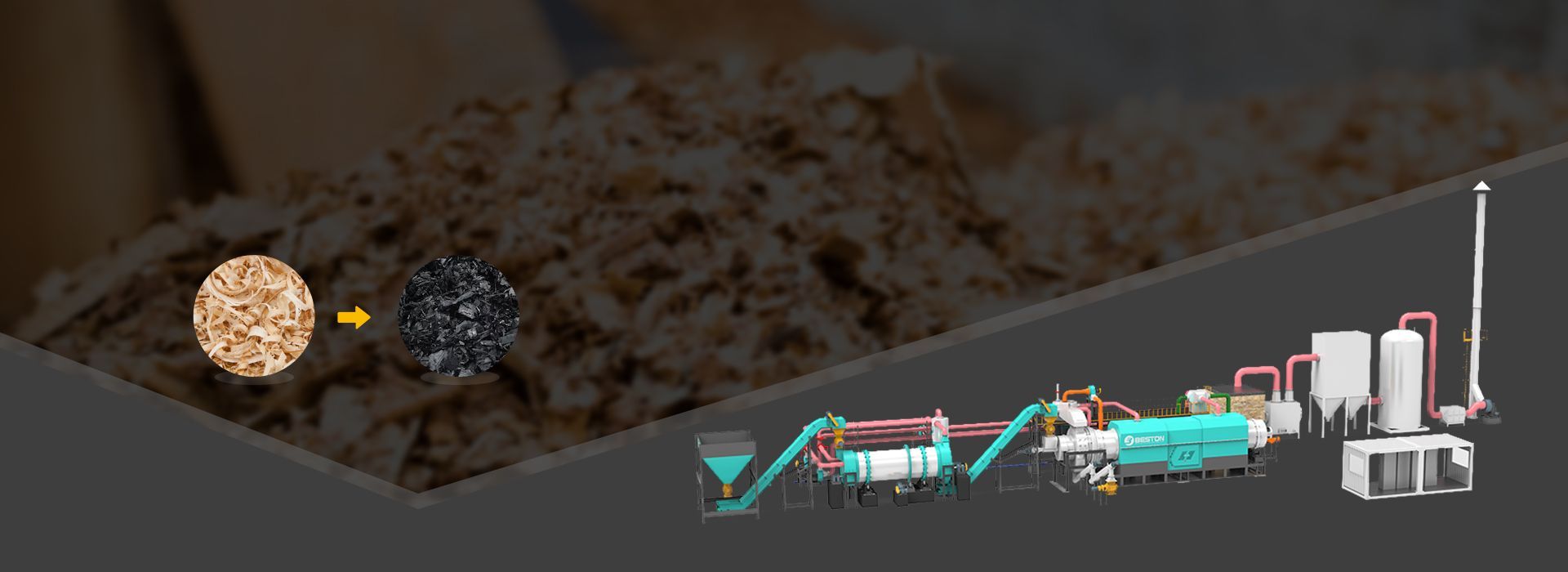
When sawdust is left to decompose in landfills, it releases methane, a potent greenhouse gas. Recycling sawdust through processes like converting it into charcoal using a sawdust charcoal machine can prevent this methane emission. Additionally, the use of sawdust - derived products instead of those made from newly - cut wood reduces the carbon footprint associated with logging, transportation, and processing of fresh timber.
Chemically - treated wood can contaminate soil and water if the sawdust from such wood is not properly managed. Recycling sawdust allows for the separation and proper treatment of potentially harmful substances. This ensures that the environment remains free from the negative impacts of chemicals leaching into the soil and water sources.
For wood - related industries, recycling sawdust can lead to significant cost savings. Instead of paying for waste disposal, companies can invest in recycling equipment like sawdust charcoal machines. The recycled products, such as charcoal briquettes made from sawdust, can be sold in the market, generating an additional revenue stream. For example, small - scale woodworking shops can turn their waste sawdust into value - added products, thus offsetting some of their production costs.
The recycling of waste sawdust has given rise to new industries and job opportunities. There are now businesses dedicated to collecting, processing, and recycling sawdust. Workers are needed to operate sawdust recycling machinery, manage the recycling process, and market the recycled products. In regions where the sawdust recycling industry has taken root, it has contributed to local economic development.
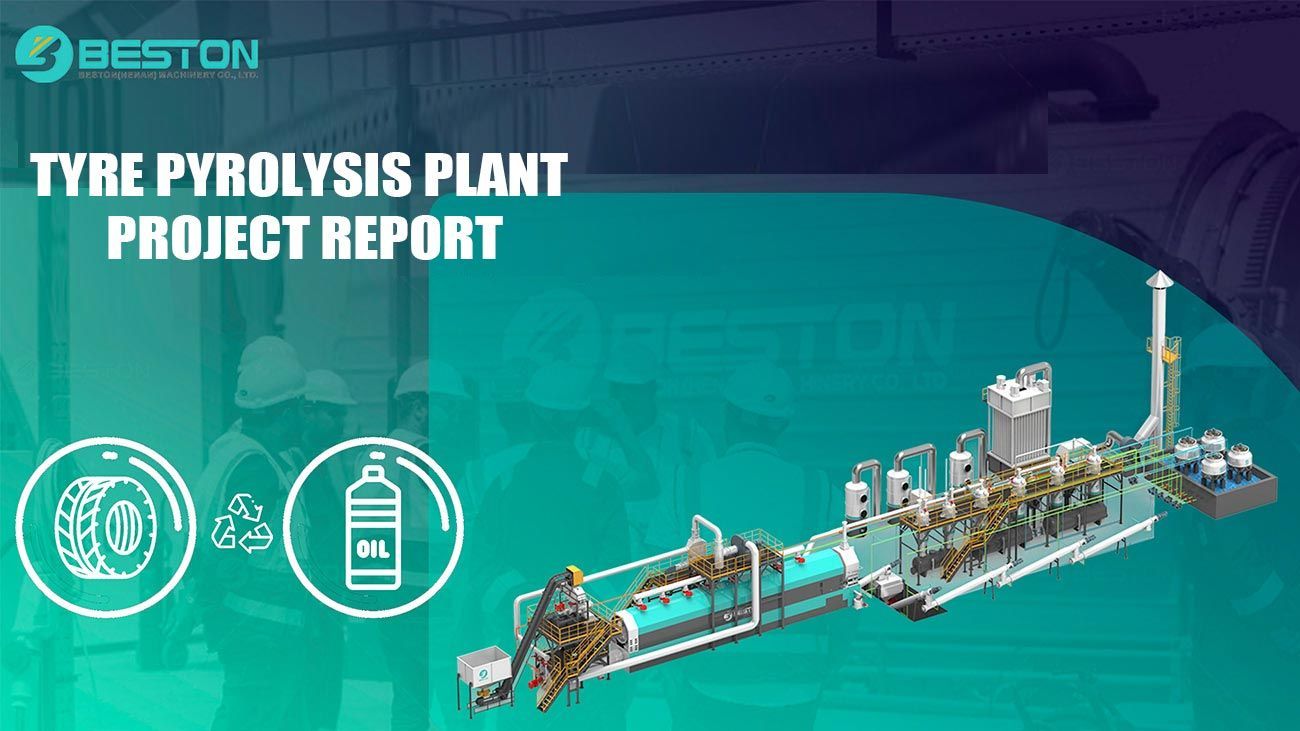
As you now are familiar with this fact, it is possible to find out what the merchandise are and why you should make a good investment of the type. Black carbon is among the interesting products, and is particularly on the go. Additionally, you will be generating a fuel that can be used to power the equipment that recycles the tires. It is possible to bank in the tyre pyrolysis plant investing in itself and its own fuel, and that is definitely one huge advantage.
The truth is, you will notice that the products pay for the equipment after which start making you serious money. What amount of cash is dependent upon how many tires you recycle. You may even end up asking other businesses with your neighborhood provided you can have their tires so that you can recycle them. If that's an alternative, why not?
Once they learn what you are doing with them, they may want a few bucks to the tires, or they might be considering the merchandise you might be producing. Either way, you're the main one with the machine, so undertaking a lot of the tires that must be recycled will help you will make more money. Isn't that really neat the best way to make that form of money through the tires you intend on recycling?
A tire pyrolysis plant is quite innovative, and you could see just why other businesses are receiving in about the deal. Maybe you can even team on top of some area businesses that will help you make this investment. You can certainly discover how it can be profitable for everyone, and it might be a community recycling effort. If you decide to go ahead and recycle the tires like a community, you might break up the profits.
You should decide the location where the tire recycling plant will be placed. You will need to evaluate which you are likely to use these products that are produced. As soon as you start seeing those tires being recycled, however, you will be really gonna like what happens next. You are likely to have a lot recycled product that you might not know where to turn.
Actually, at that time you will know specifically where to make, and you will be turning a return. Should you look into the businesses that want these fuels, it can be clear why they use them. They need them over and over, and you could provide them after recycling tires again and again. Now you simply need to discover which manufacturer you are going to count on in order to get the plant you require set up.
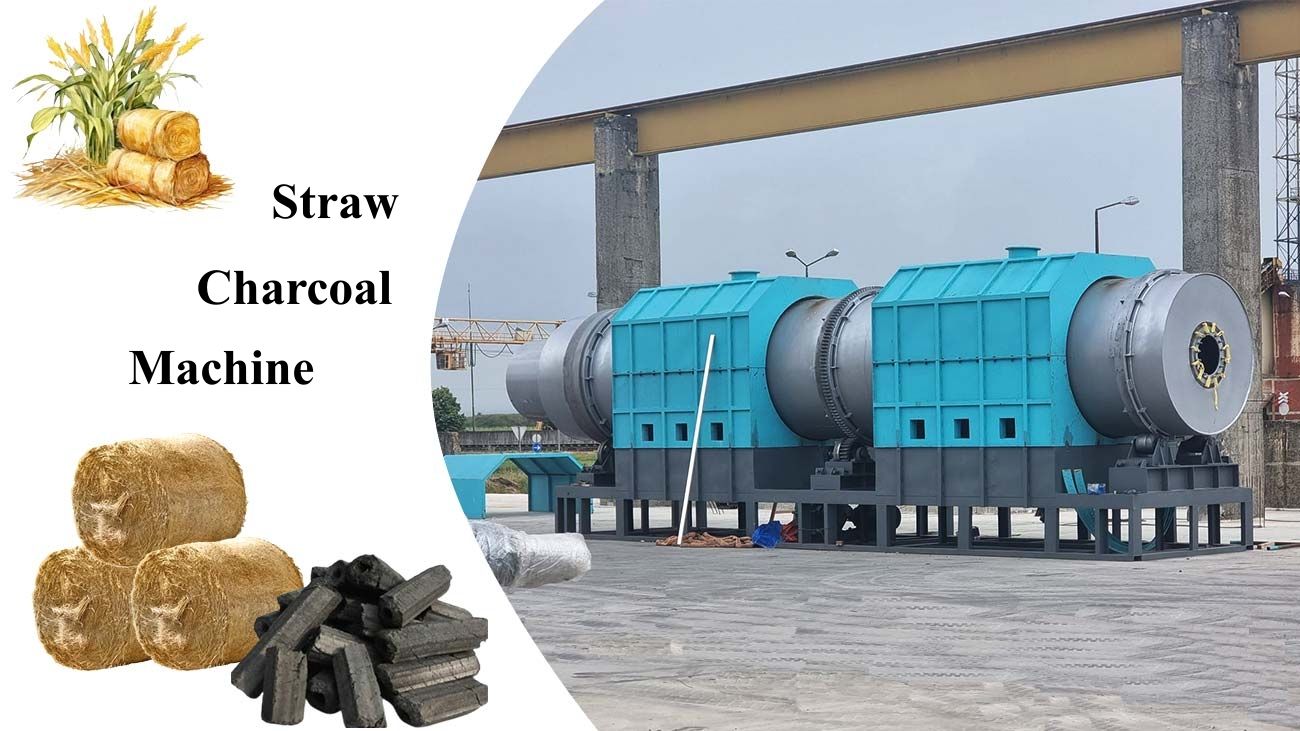
In the quest for more efficient and sustainable charcoal production, modern charcoal machines have adopted innovative designs to enhance their continuous operation time. Among these advancements, two unique features stand out: the elimination of wood vinegar and tar collection through insulation and the integration of a nitrogen purging system to prevent pipeline blockages. Let's explore these designs in detail.
1. Insulation for Eliminating Wood Vinegar and Tar Collection
One of the primary challenges in charcoal production is the collection of byproducts like wood vinegar and tar, which can disrupt the continuous operation of the charcoal machine. Traditional systems often require regular maintenance and cleaning to manage these byproducts, leading to downtime.
To address this issue, some modern charcoal machine utilize a unique insulation design. By effectively insulating the internal components, these machines maintain optimal temperatures during the carbonization process. This insulation minimizes the condensation of wood vinegar and tar within the system, allowing for their effective combustion within the machine itself. As a result, operators can experience longer run times without the need for frequent cleaning or maintenance associated with these byproducts.
2. Nitrogen Purging System for Preventing Pipeline Blockages
Another innovative design to enhance the continuous operation of charcoal machines is the incorporation of a nitrogen purging system. Pipeline blockages can occur due to the accumulation of carbonized material or condensation, which disrupts the flow of gases and reduces the efficiency of the operation.
The nitrogen purging system provides a solution by introducing nitrogen gas into the pipelines, effectively clearing any obstructions. This system operates automatically, detecting potential blockages and activating the purging process as needed. By maintaining clear pathways for gases, the nitrogen purging system ensures that the charcoal machine can operate continuously without interruptions caused by blockages. This not only enhances productivity but also contributes to the overall efficiency of the charcoal production process.
Conclusion
The advancements in charcoal machine design, particularly the elimination of wood vinegar and tar collection through insulation and the integration of a nitrogen purging system, represent significant strides toward more efficient and continuous operation. These innovations not only reduce maintenance downtime but also enhance the overall productivity of charcoal production. As the industry continues to evolve, such unique designs will play a crucial role in achieving sustainable and efficient charcoal manufacturing practices.
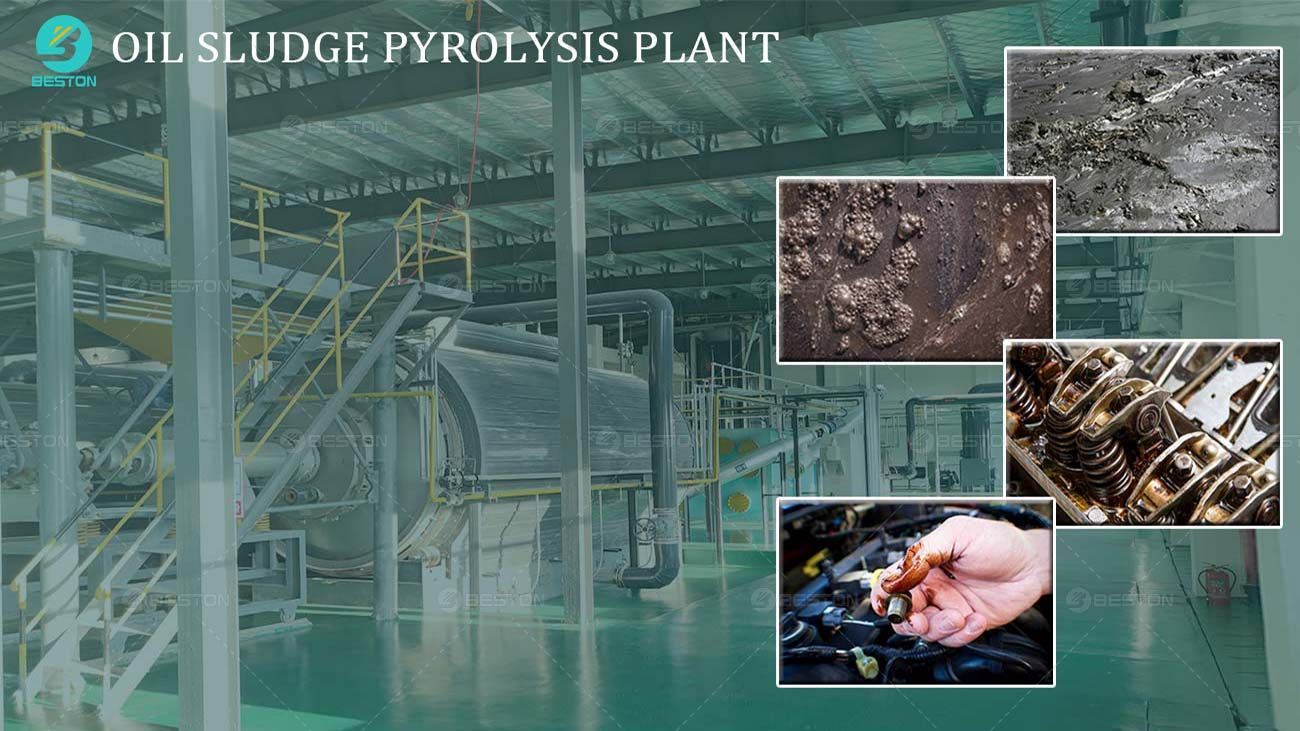
Oil sludge, a byproduct of oil extraction and refining, poses significant environmental challenges due to its complex composition, which often includes harmful hydrocarbons and heavy metals. Traditional disposal methods can lead to soil and water contamination, making the need for safe and effective treatment crucial. One promising solution is the use of Thermal Desorption Units (TDUs). This article explores why TDUs are effective for the harmless treatment of oil sludge.
What is Thermal Desorption?
Thermal desorption is a process that uses heat to remove contaminants from solid or semi-solid materials. In the context of oil sludge, TDUs heat the sludge to elevated temperatures in a controlled environment, facilitating the evaporation of volatile organic compounds (VOCs) and other harmful substances. The cleaned material can then be safely disposed of or reused.
Why TDUs Are Effective for Oil Sludge Treatment
Efficient Contaminant Removal: Thermal desorption unit effectively vaporize harmful hydrocarbons and other volatile compounds present in oil sludge. The heat causes these contaminants to evaporate, allowing for their capture and treatment, significantly reducing the toxic load of the sludge.Controlled Process: The thermal desorption process is conducted in a controlled environment, minimizing the risk of releasing harmful substances into the atmosphere. Advanced emission control technologies are often integrated into TDUs to filter and treat any gases produced during the process.
Versatility: TDUs can treat a wide variety of oil sludge compositions, making them suitable for different industries, including oil and gas, petrochemicals, and manufacturing. This adaptability allows for the effective handling of various types of waste.
Volume Reduction: By removing volatile components, TDUs significantly reduce the volume of oil sludge, making it easier and more cost-effective to manage. The resulting solid residue can often be safely disposed of or repurposed.
Resource Recovery: The thermal desorption process can recover usable products, such as oil and gas, from the treated sludge. This not only minimizes waste but also helps recover valuable resources, contributing to a more sustainable approach to waste management.
Compliance with Regulations: The use of TDUs aligns with environmental regulations that mandate the safe treatment and disposal of hazardous materials. By effectively reducing harmful substances, TDUs help facilities meet regulatory requirements and avoid potential fines.
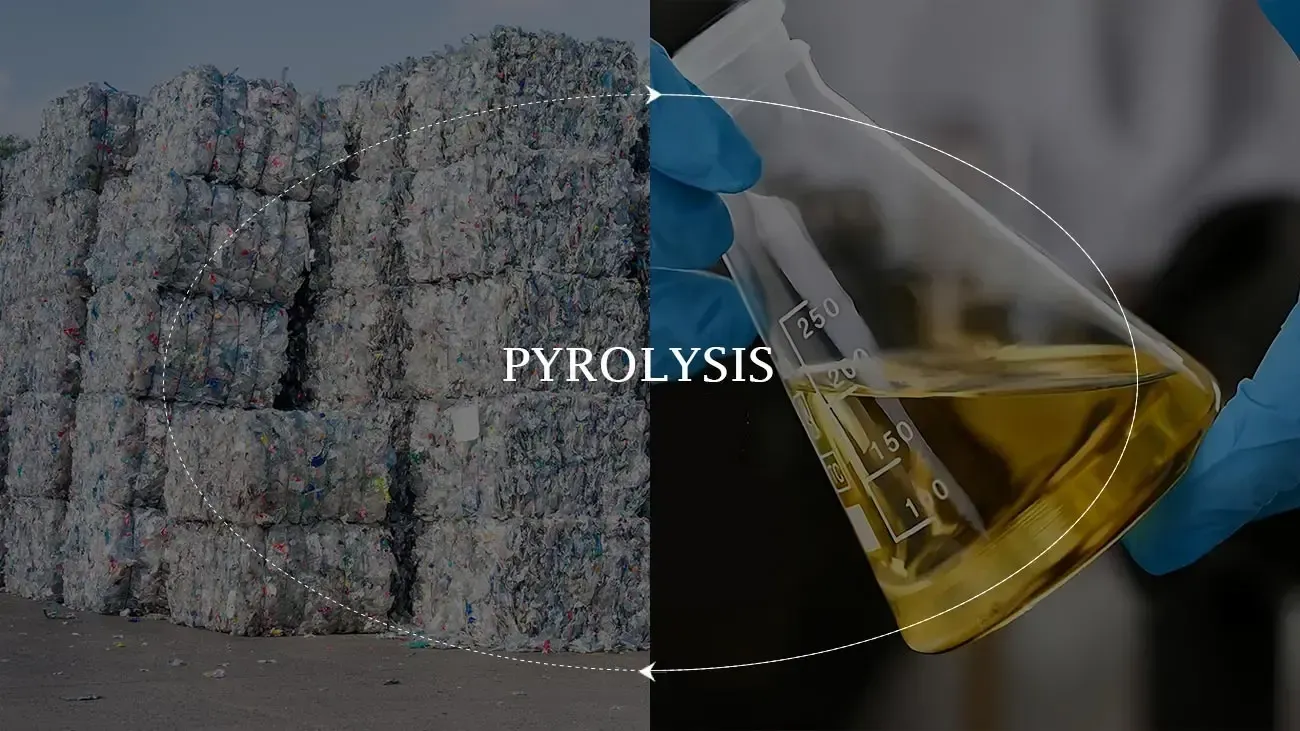
Evaluating the plastic pyrolysis process to determine if it is correctly clarified involves a thorough analysis of several key factors. Pyrolysis is a thermal decomposition process that breaks down plastic waste into valuable byproducts like oil, gas, and char, under controlled conditions of temperature and pressure. Properly assessing this process is crucial to ensure that it meets environmental standards and efficiently converts plastic waste.
First, understanding the feedstock characteristics is essential. The type and quality of plastic waste influence the pyrolysis process. Plastics with different polymer compositions and contaminants can affect the efficiency and output of the process. It is important to evaluate whether the plastic feedstock is properly sorted and cleaned before entering the pyrolysis system.
Next, the reactor design and operating conditions must be scrutinized. The reactor's design affects heat transfer and material residence time, which are critical for efficient pyrolysis. The operating temperature, typically ranging from 300°C to 700°C, must be maintained consistently to ensure complete breakdown of plastic polymers. Variations in temperature can lead to incomplete pyrolysis or the formation of undesirable byproducts. Additionally, the pressure within the reactor can impact the quality of the output products, so it is important to monitor and control these parameters precisely.
The efficiency of the pyrolysis process is also linked to the type of catalyst used, if any. Catalysts can enhance the breakdown of complex polymers and improve the yield and quality of the resulting oil and gas. Evaluating the catalyst's effectiveness and whether it is being used correctly is a key part of assessing the process.
Post-processing and product handling are equally important. The separation and purification of the pyrolysis products, such as oil, gas, and char, should be effectively managed to ensure high-quality outputs. Any residual contaminants or impurities in the products can affect their usability and market value. Therefore, evaluating the processes involved in product handling and purification is necessary to confirm that the system is functioning correctly.
Environmental impact assessment is another crucial aspect. Properly clarified pyrolysis systems should minimize emissions and handle byproducts responsibly. Evaluating the emission control systems and waste management practices is essential to ensure compliance with environmental regulations and standards. This includes checking for the presence of any harmful emissions and verifying that they are being treated or filtered effectively.
Finally, reviewing operational and maintenance practices is important to ensure the longevity and reliability of the pyrolysis system. Regular maintenance, calibration, and monitoring are required to keep the system running efficiently and to address any issues promptly. Evaluating these practices helps confirm that the system is not only clarified but also operates smoothly and effectively over time.
In conclusion, evaluating whether the plastic pyrolysis process is correctly clarified involves a comprehensive review of feedstock quality, reactor design and operating conditions, catalyst use, product handling, environmental impact, and operational practices. A well-clarified process ensures efficient plastic waste conversion, high-quality products, and minimal environmental impact, making it a crucial aspect of modern waste management and recycling strategies.
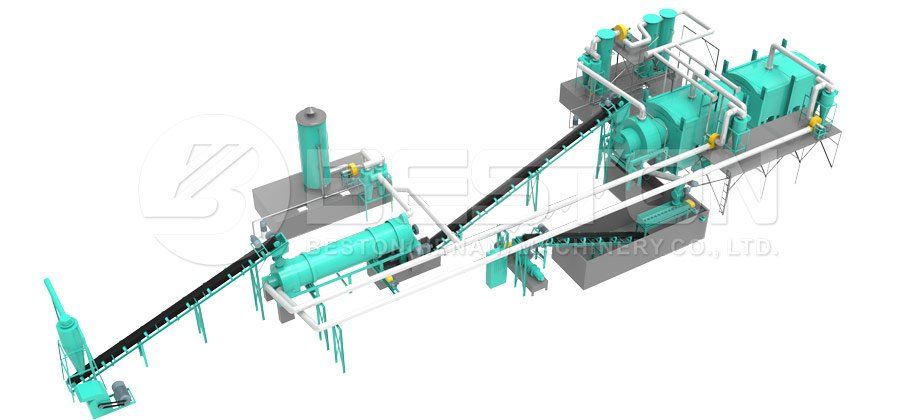
How Is Biomass Converted Into Fuel?
Biomass may be transformed into fuel easily. It is going through a process called pyrolysis. It is heated to a temperature where material will break up. Precisely what is left is liquid and solid fuel. What is solid is called charcoal. This can be sold to people and businesses around the world. The liquid material bring a lubricant or might even be purchased by cosmetic companies. It does not burn since the oxygen will not be in the reactor when it is heating up. If you have a lot of biomass, you are going to definitely want to identify a company that can sell you one for less.
How To Find Companies That Sell The Products?
Locating firms that sell these items is easier than ever before. Element of this is because more companies are selling them available for purchase. It is additionally easier to find them due to the web. You will discover company websites that will showcase a number of their carbonizer machine . You do have to evaluate them to ensure that they can be large enough to take care of every one of the biomass you must process. Other facts to consider include the type of energy it uses to power the system. Also look at the several types of biomass that could be processed. This all information can assist you make the right decision when obtaining one from all of these businesses.
Alternative Methods To Gauge These Appliances
There are numerous things to consider. To start with, you should think about its size. The greater the unit is, the better fuel that will produce. Consider the type of customers that you will have with this business. Charcoal may be sold to regular people, different industries, and also the agricultural market. The machines should be the right size for your personal facility. You need to have enough room to house them. Consider the expense of shipping and exactly how long it should take to reach. These are generally all factors that really must be considered before making your purchase.
Getting a biomass carbonization machine can be accomplished within hours. You need to spend some time to obtain the companies and in the end evaluate them in relation to production and expense. When they are shipped to you, they must take no more than a couple of days to put together. When they are fully functional, you can expect to never have to worry about access biomass at your facility. It would simply be transformed into a marketable product that will help your organization grow.
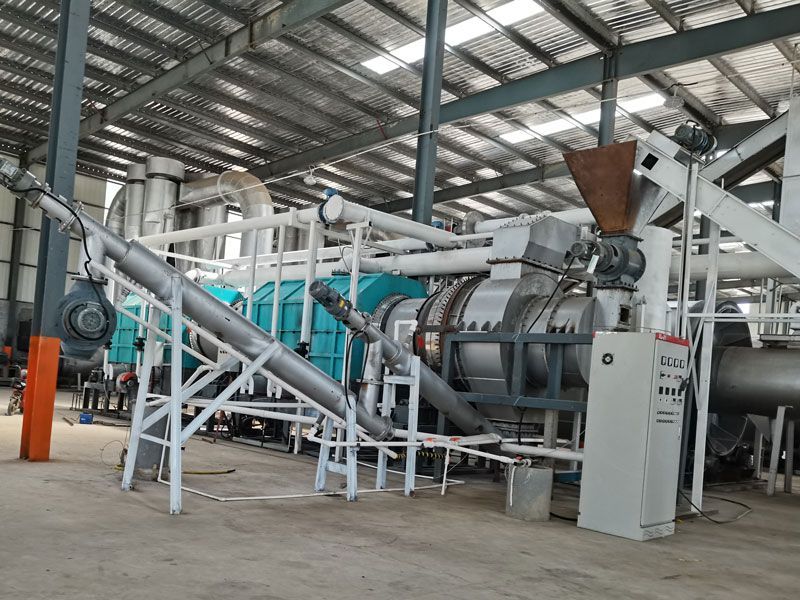
Biomass describes raw materials that are widely used to produce charcoal. Such as:
- Sludge
- Agricultural residues such as coconut shells, coconut husks, straw, and various other green agricultural waste
- Wood from woodlands and natural forests
What Does A Biomass Pyrolysis Plant Do?
The biomass pyrolysis plant , that goes with the names of Biochar Pyrolysis Machine or Biomass Carbonization Plant, serves the goal of producing charcoal from raw materials called biomass. This really is made possible through high-temperature heating. The charcoal made out of biomass offers many applications across several industries.
In the industry of agriculture, biochar is frequently used to increase the conditions of soil that help to facilitate harvesting. In other industries, the charcoal is utilized as being a steel-coating agent, activated charcoal, or like a fuel. Biochar can also be used as Shisha charcoal or perhaps for BBQs
The Functions From The Biomass Pyrolysis Plant
The Biomass Pyrolysis Plant includes a double-layer design, which ensures that the reduced portion of these appliances is within constant exposure to the hot air. The style of these plants will also help to maximize heat use efficiency from beginning to end.
The desulfurization steam and smoke abatement are cooled off from a condenser, which ensures there is not any gas pollution and this these plants match to the environmental protection standards.
During the entire production processes, the combustible gas produced is minimal. The gas which is produced is moved with a fan to supply heat for the pyrolysis furnace, which will help in order to save significantly on energy costs.
These machines only use a single source for producing hot air, which helps to save on overall costs.
This particular pyrolysis technology can perform reducing combustible waste volumes by 95% or more.
Usually the one-fire two-step method adopted by these machines is actually a unique and innovative technology.
Other Applications Of Pyrolysis Plants
Carbonizing biomass not only deals with Biomass Waste but can also be used to dispose of other wastes like medical waste, oil sludge, rubber, tires, plastic, municipal solid waste and much more. Through the procedure of pyrolysis, this type of waste is effectively changed into useful resources like fuel oil, steel wire, carbon black and much more.
Influenced by the temperature and thermal environment, pyrolysis mainly yields biochar at temperatures below 450 degrees, if the rate of heating is gradual and primarily gases if the temperature exceeds 800 degrees, using heating rates that happen to be more rapid.
Pyrolysis works well with both large and small scale locations and is a wonderful means to get rid of unwanted waste. In addition, it provides a favorable and flexible strategy to convert biomass in a solid form into easily transported and stored liquids, which can be often then utilized for producing chemicals, power, and heat.
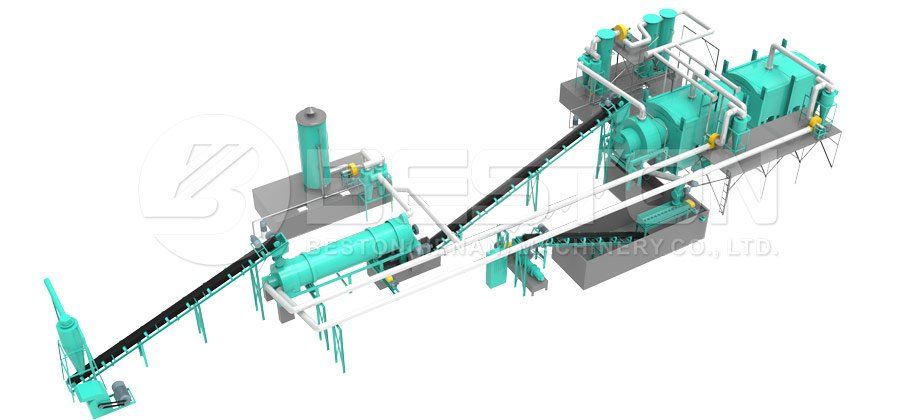
In a continuous sawdust charcoal machine , recycling sawdust into charcoal takes from twenty to thirty minutes. This is caused by why the reaction happens in a completely oxygen free environment making it faster and in addition, a good deal safer. These furnaces can be bought in a wide array of capacities starting from half a ton hourly to a lot more than 3 ton each hour. In addition to sawdust, this equipment is also suitable for converting bamboo, coconut shells, rice husk as well as other waste materials into charcoal.
The procedure of converting sawdust or other materials into charcoal is pretty simple. Before sawdust is pushed into the furnace, it must be ensured how the moisture content articles are below 20%. When the moisture content articles are high, the process can take a lot longer and the grade of the finished product will not be as great as the item created from raw material with moisture content below 20%. Therefore, a dryer should be used to bring down the moisture content.
In the next step, this dry raw material is pushed from the carbonization furnace. The temperature from the furnace keeps increasing constantly as well as the raw material is converted into combustible gas and sawdust charcoal. Modern machines on the market today take advantage of various tools to capture this combustible gas. Another tool within this machine gets rid of sulfur within the gas. After purification, you will have the option of converting this gas into wood vinegar and tar. Tar is really a waterproof material which is used in a variety of industries because of its high corrosion and wear resistance. Similarly, wood vinegar as traditionally used in food preservatives and it likewise has anti-inflammatory properties which means furthermore, it has medicinal uses.
The sawdust charcoal created in the carbonization furnace is generally too hot to be handled manually. Because of this ,, modern machines come provided with a air conditioning to take across the temperature from the charcoal for even more processing.
With regards to buying a sawdust charcoal making machine is concerned, there are some what exactly you need to consider to get the very best bang for your buck. One of the most important what exactly you need to consider is the efficiency in the machine. It is suggested to decide on a unit that is equipped with a continuous carbonization furnace. Continuous operation is cost efficient and labor efficient. It must also use advanced technology to take care of a lot of the processes automatically.
Another significant parameter you need to examine is definitely the operational capacity from the machine. It is determined by the accessibility of raw material and need for the finished product with your location. Additionally you need to consider the power requirements. Modern machines can typically be powered through a wide variety of fuels such as biomass, natural gas, diesel, wood or charcoal among other options.
Overall, a sawdust charcoal making machine is a good investment when you have ready option of sawdust and also other biomass material for conversion into charcoal. Keep the aforementioned tips under consideration and get a contemporary machine rich in efficiency to obtain the most bang for your buck.Benefits Of A Sawdust Charcoal Making Machine
When you have entry to a large amount of sawdust that may be just going waste, a good way to help you this otherwise waste material is usually to convert it into charcoal. Charcoal is really a highly efficient fuel and also has numerous types of other uses such as in beauty industry and food industry and the like. Converting sawdust into charcoal is not difficult with the aid of a sawdust charcoal making machine.
Within a continuous carbonization furnace, recycling sawdust into charcoal takes from twenty to thirty minutes. This is due to the reason why the reaction occur in a completely oxygen free environment rendering it faster as well as, a good deal safer. These furnaces are available in a variety of capacities which range from half a ton hourly to greater than 3 ton per hour. In addition to sawdust, this equipment is also appropriate for converting bamboo, coconut shells, rice husk and various other waste matter into charcoal.
The whole process of converting sawdust or another materials into charcoal is rather simple. Before sawdust is pushed into the furnace, it needs to be ensured that this moisture content is below 20%. In case the moisture content is high, the method can take a lot longer and the grade of the finished product will never be just like this product made from raw material with moisture content lower than 20%. Therefore, a dryer should be utilized to bring down the moisture content.
Within the next step, this dry raw material is pushed inside the carbonization furnace. The temperature in the furnace keeps increasing constantly and also the raw material is transformed into combustible gas and sawdust charcoal. Modern machines available today take advantage of various tools to capture this combustible gas. Another tool in this machine removes sulfur from the gas. After purification, you will have the choice of converting this gas into wood vinegar and tar. Tar is actually a waterproof material which is used in different industries because of its high corrosion and wear resistance. Similarly, wood vinegar as commonly used in food preservatives and in addition it has anti-inflammatory properties meaning additionally, it has medicinal uses.
The sawdust charcoal produced in the carbonization furnace is typically too hot to become handled manually. This is why, modern machines come provided with a cooling system to take on the temperature of the charcoal for more processing.
So far as purchasing a sawdust charcoal making machine is involved, there are some things you need to think about to acquire the most effective value for your money. One of the more important what exactly you need to check out is definitely the efficiency from the machine. It is suggested to choose a piece of equipment that is equipped with a continuous carbonization furnace. Continuous operation is cost efficient and labor efficient. It must also employ advanced technology to deal with a lot of the processes automatically.
Another necessary parameter you should take a look at is the operational capacity of your machine. It depends on the accessibility to raw material and demand for the finished product within your location. Additionally you need to consider the ability requirements. Modern machines can typically be powered through numerous fuels including biomass, natural gas, diesel, wood or charcoal among additional options.
Overall, a sawdust charcoal making machine is a great investment if you have ready option of sawdust and also other biomass material for conversion into charcoal. Keep those tips under consideration and purchase a modern machine rich in efficiency to get the most value for your money.
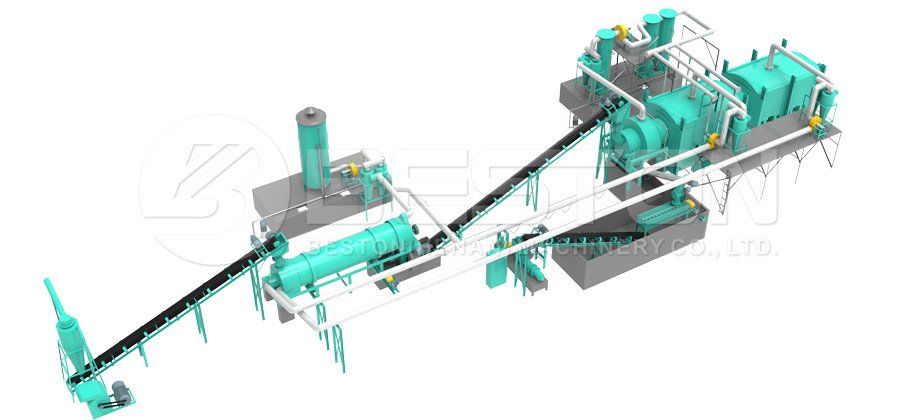
You have to find reviews on the bamboo charcoal making machine before you buy it so do you know what other people thought of it. If you realise a device that has a lot of positive reviews, you already know that it will likely be worth your money to buy. But, should you don't buy something which is well reviewed, you could end up regretting it if it doesn't work as it should for you personally. It simple to check over reviews so don't go with a random machine so that you don't turn out regretting your purchase.
Before you purchase a machine, be sure it's being offered for a good price. There are tons of several machines out there which are different prices therefore it pays to purchase around a little bit. You don't have to get saddled with a thing that costs a lot more than exactly what is fair because you may then find yourself planning to send it back to have your money back so you can get a much better deal on this sort of machine. Either way, it's best to think about such a few companies are charging in order to work together with one which provides the best deals on his or her machines.
Ask a company provided you can return a piece of equipment for them to have your money back if you're unhappy with it. That, or maybe you should at least be capable of getting another one brought to you. If anything you don't want to do business with an organization that will make you continue a thing that you're not likely to use since it has many issues going on with it. It's readily accessible out in case a company accepts returns, just check their site of course, if they don't possess the information there you are able to contact them on the telephone.
See what you can find in the way of used machines in order to save a little money. It's vital that you get a machine that may be in good working order. But, if you simply want to invest in a couple for parts and after that use those parts to construct a fresh machine, you might be able to pull off buying machines which are broken in a different way. Figure out what for you to do with the machines you're planning on buying used and it must be a little easier to know which of them to purchase.
Now you have an idea of what you need to do when you want to buy a bamboo charcoal machine for any decent price. It's an issue that will remember to do right but it is worth it ultimately when investing in something which is effective.
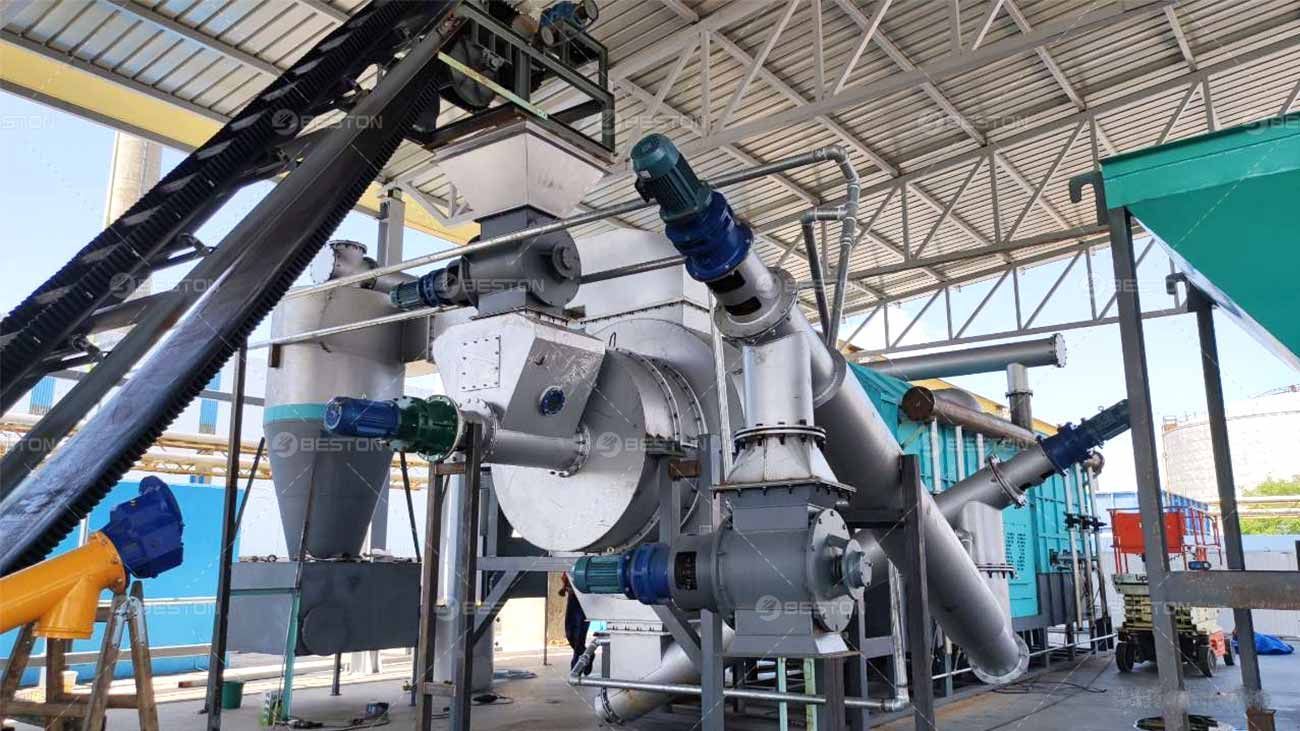
Charcoal has been a crucial energy source for centuries, traditionally made through slow-burning wood in earth-covered pits. While effective, this old-fashioned method often leads to heavy smoke emissions, low efficiency, and environmental degradation due to deforestation and air pollution. In recent years, a modern way of charcoal production has emerged, offering a cleaner, more sustainable, and efficient approach that meets both industrial demands and environmental standards.
At the heart of this modern transformation is the biomass pyrolysis technology. Unlike the traditional methods that rely on uncontrolled burning, modern charcoal production uses specialized equipment known as biomass carbonization machines. These machines operate under a condition of limited oxygen, turning organic waste such as wood chips, coconut shells, bamboo, sawdust, and even agricultural residues into high-quality charcoal through a process called pyrolysis. This process not only reduces emissions but also ensures a higher yield and consistent quality of the final product.
One of the most striking advantages of modern charcoal production machine is its eco-friendly nature. During pyrolysis, volatile substances are released in the form of combustible gas, which can be collected and reused as a heating source within the system. This closed-loop design not only saves energy but also minimizes the release of harmful gases into the atmosphere. Some advanced systems are even equipped with flue gas purification systems that filter out dust and harmful components, ensuring compliance with increasingly strict environmental regulations.
Furthermore, modern charcoal production has opened the door to the circular economy. Instead of cutting down trees, many producers now use waste biomass materials, giving a second life to what was once considered worthless. This not only reduces pressure on forests but also offers a profitable way to manage agricultural and forestry residues. For regions with abundant biomass waste, such as palm shells, rice husks, or sugarcane bagasse, charcoal production becomes an efficient method of waste-to-energy conversion.
The economic potential of this modern process is another reason it is gaining popularity worldwide. From small-scale producers to large industrial facilities, the demand for biochar is growing in various fields such as agriculture, metallurgy, water purification, and even cosmetics. The versatility and high calorific value of modern charcoal make it a desirable alternative to fossil fuels in many applications.
With the help of automation, the entire production process has become safer and more labor-efficient. Modern charcoal machines are often equipped with PLC control systems, allowing for precise temperature regulation, moisture monitoring, and production tracking. This level of control helps ensure consistent product quality and reduces operational risks.
As the world continues to seek sustainable solutions to energy and waste challenges, modern charcoal production represents a practical and forward-thinking approach. It reflects how innovation can transform traditional industries into environmentally responsible enterprises. Whether you're an investor, an environmentalist, or simply someone interested in renewable energy, the evolution of charcoal production is a compelling example of how technology can drive positive change.
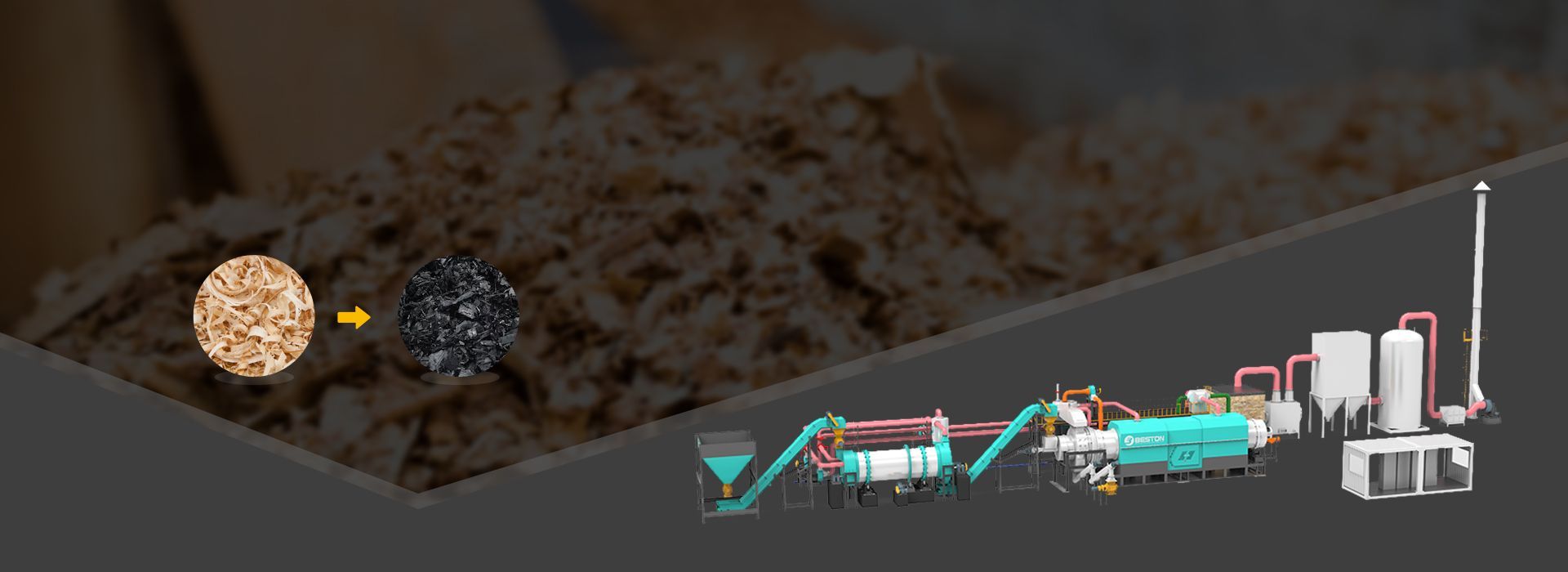
When sawdust is left to decompose in landfills, it releases methane, a potent greenhouse gas. Recycling sawdust through processes like converting it into charcoal using a sawdust charcoal machine can prevent this methane emission. Additionally, the use of sawdust - derived products instead of those made from newly - cut wood reduces the carbon footprint associated with logging, transportation, and processing of fresh timber.
Chemically - treated wood can contaminate soil and water if the sawdust from such wood is not properly managed. Recycling sawdust allows for the separation and proper treatment of potentially harmful substances. This ensures that the environment remains free from the negative impacts of chemicals leaching into the soil and water sources.
For wood - related industries, recycling sawdust can lead to significant cost savings. Instead of paying for waste disposal, companies can invest in recycling equipment like sawdust charcoal machines. The recycled products, such as charcoal briquettes made from sawdust, can be sold in the market, generating an additional revenue stream. For example, small - scale woodworking shops can turn their waste sawdust into value - added products, thus offsetting some of their production costs.
The recycling of waste sawdust has given rise to new industries and job opportunities. There are now businesses dedicated to collecting, processing, and recycling sawdust. Workers are needed to operate sawdust recycling machinery, manage the recycling process, and market the recycled products. In regions where the sawdust recycling industry has taken root, it has contributed to local economic development.
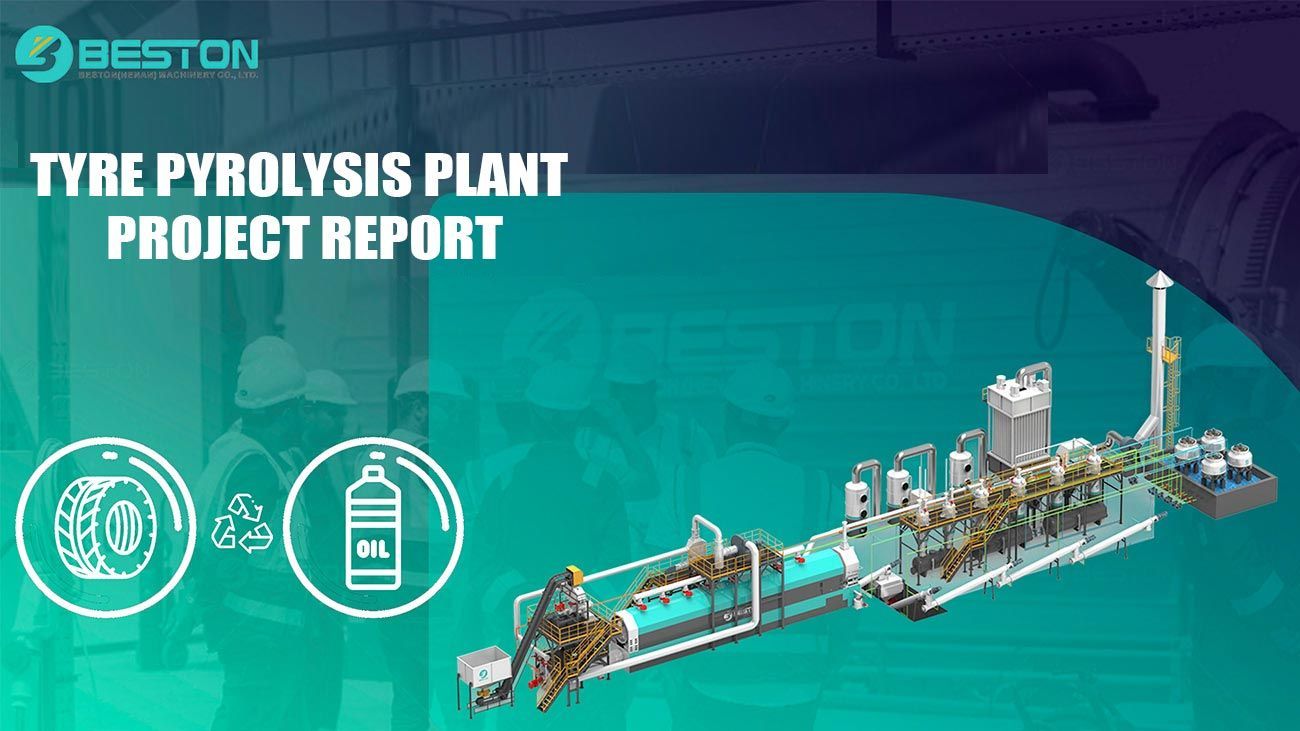
As you now are familiar with this fact, it is possible to find out what the merchandise are and why you should make a good investment of the type. Black carbon is among the interesting products, and is particularly on the go. Additionally, you will be generating a fuel that can be used to power the equipment that recycles the tires. It is possible to bank in the tyre pyrolysis plant investing in itself and its own fuel, and that is definitely one huge advantage.
The truth is, you will notice that the products pay for the equipment after which start making you serious money. What amount of cash is dependent upon how many tires you recycle. You may even end up asking other businesses with your neighborhood provided you can have their tires so that you can recycle them. If that's an alternative, why not?
Once they learn what you are doing with them, they may want a few bucks to the tires, or they might be considering the merchandise you might be producing. Either way, you're the main one with the machine, so undertaking a lot of the tires that must be recycled will help you will make more money. Isn't that really neat the best way to make that form of money through the tires you intend on recycling?
A tire pyrolysis plant is quite innovative, and you could see just why other businesses are receiving in about the deal. Maybe you can even team on top of some area businesses that will help you make this investment. You can certainly discover how it can be profitable for everyone, and it might be a community recycling effort. If you decide to go ahead and recycle the tires like a community, you might break up the profits.
You should decide the location where the tire recycling plant will be placed. You will need to evaluate which you are likely to use these products that are produced. As soon as you start seeing those tires being recycled, however, you will be really gonna like what happens next. You are likely to have a lot recycled product that you might not know where to turn.
Actually, at that time you will know specifically where to make, and you will be turning a return. Should you look into the businesses that want these fuels, it can be clear why they use them. They need them over and over, and you could provide them after recycling tires again and again. Now you simply need to discover which manufacturer you are going to count on in order to get the plant you require set up.